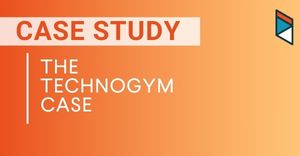
An effective and efficient logistics planning? A better lifestyle.
The Customer – Technogym
Technogym – An Italian company, a global leader in the production of equipment for sports and leisure, promoting movement and well-being both locally and globally.
Their mission: to encourage as many people as possible to adopt a lifestyle that includes physical activity, healthy eating, and a positive mental approach.
Why Load Manager?
The starting point often lies in pausing and analyzing the present, becoming aware of one’s strengths and weaknesses. By analyzing internal company processes, it becomes clear that there are often areas for improvement. This was the starting point for our client, who, by mapping and examining their business processes, discovered that some activities, more obsolete and/or manual, could be transformed to become more effective and efficient.
So, why Load Manager? In order to streamline logistical processes, and more, while enhancing activities.
“With the way the loading and unloading activities were initially organized, we were never aware of when the vehicle would arrive at the warehouse. The communicated information was therefore superficial and not practically useful for planning activities” – Technogym’s Logistics Coordinator.
There was, therefore, a desire to make the work process more fluid, eliminating the excessive flow of emails. The original needs were:
- to eliminate triangulation between the logistics team, shippers, carriers, and the loading department;
- to reduce human errors;
- to have a more linear and effective loading schedule;
- to reduce and monitor loading wait times.
“Load Manager, in addition to being a useful tool for booking and planning, allows us to monitor our performance and that of our suppliers. In fact, we can track and control how many minutes/hours we spend preparing the bay and, at the same time, measure when a vehicle arrives early or late compared to the booking.”
Download the complete case study for free!